The first surface treatment is the anti-corrosion treatment. The aim is to ensure the integrity of the structure and to ensure that it will not deteriorate over time. Steel when exposed to open air and moisture will oxidize over time and form rust. Rusty steel crumbles and weakens the structure until it ruptures.
There are different ways to fight corrosion, the most common being galvanization. Galvanizing is a chemical process that consists of depositing a layer of zinc on steel.
Zinc is a metal that oxidizes quickly in the presence of oxygen and forms zinc oxide crystals. It is he who will oxidize and not the steel on which it is deposited. This zinc oxide is very stable and forms a barrier that prevents oxygen from coming into contact with steel.
There are several ways to deposit this zinc onto the surface of the steel. The most common are:
By electrodeposition: the parts are dipped in a solution containing zinc ions and an electric current is passed between the parts and the bath. Zinc ions settle on the surface of the parts. The advantage of this solution is that it is quite economical and produces smooth parts, but the disadvantages are numerous: the thickness of the zinc layer is low and the inside of the tubes are not galvanized, the electrical charge remaining on the surface. As a result, corrosion protection is lower: a slight impact or slight wear and tear may be sufficient to damage the protection. In addition, since the inside of the tubes is not protected, rust forms inside and over time weakens the parts.
By spraying paint: anti rust paints containing zinc can be used which are either applied directly or sprayed onto steel surfaces. Here again, the big disadvantage is that the adherence of the paint on the steel is not always very good and it is not easy to paint hard-to-reach areas such as tubes.
by hot-dip galvanizing: the zinc melts at a temperature of 450°C. There are companies that specialize in hot-dip galvanizing and have molten zinc baths (furnaces). The parts are dipped directly into these baths (as shown in the picture above). An alloy of zinc and steel is formed on the surface of the parts, both inside and outside. This process is the most efficient because the zinc layer is the thickest. The inside and outside of the parts are treated to ensure excellent durability. The disadvantage is that the parts must not have any closed tubes (they explode when soaked in molten zinc). Parts coming out of hot-dip galvanizing may show drips and must be brushed and polished, which requires more work.
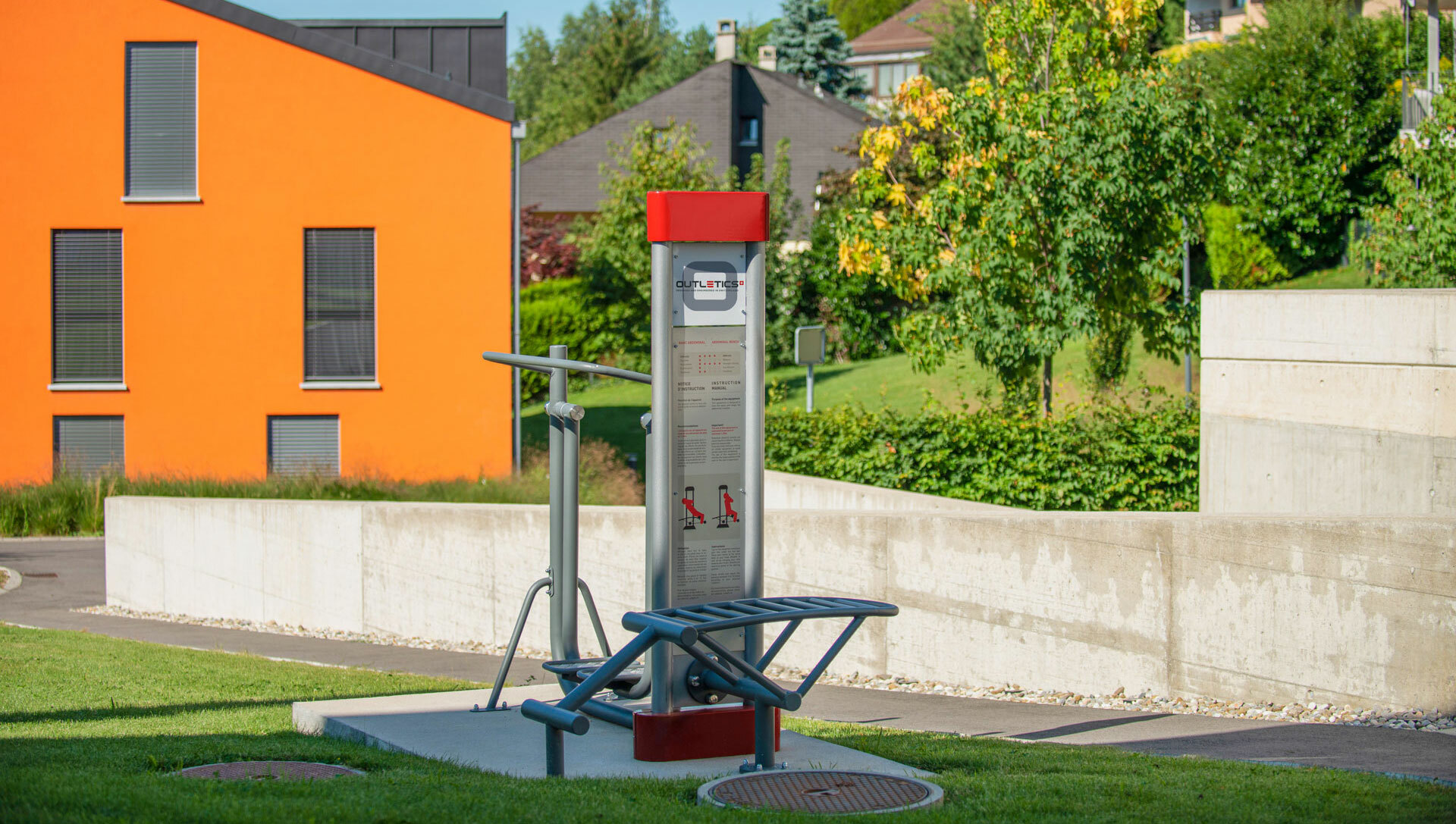
What about the outdoor fitness machines produced by Outletics?
You guessed it. At Outletics we do not compromise on quality. All our parts that are not made of stainless steel or aluminium (that do not oxidise) are hot-dip galvanized. This is what allows us to ensure the robustness and longevity of our machines, whether they are in the rain, buried in the snow or placed in the humidity of the lakeside! Outletics offers a 25-year warranty on its galvanized steel parts. All this to ensure the durability of your investment!